Stop skinning your knuckles on crazy-tight SRAM DUB crank bolts
Cheater bars, impact wrenches, and inner tubes all work, but none of them actually solve the problem. This does.
It’s been more than 5 1/2 years since SRAM first introduced its Durable Unified Bottom Bracket system, better known as DUB (sorry, I don’t know what happened to the second “B”, either). The idea behind it is sound enough: by using a 28.99 mm-diameter crankset spindle (seriously, that’s the official spec) instead of a 30 mm one, SRAM can use slightly larger bearing balls to improve durability while also making it more feasible to run an oversized spindle in a PF86 shell.
Ok, fine.
It wasn’t long after that, however, that we started hearing stories from people who couldn’t get those DUB cranks off of their bikes because the installation bolt was so damned tight. Countless internet memes followed, along with all sorts of suggestions on how to deal with it: huge breaker bars and pipes; impact guns; wooden blocks and standing on wrenches; and most recently, wrapping an inner tube around a hex wrench and the crankarm to progressively add force until the thing finally breaks loose.
I’ve opted for the leverage approach myself, where I brace the non-driveside crankarm inside a long section of galvanized steel conduit (I wrap the arm with a rag first), and then apply a similarly long breaker bar with an 8 mm impact-rated bit to the crank bolt. I pull on the pipe while simultaneously pushing on the breaker bar, and I have yet to encounter a SRAM DUB bolt that won’t yield. Physics is glorious.
Here’s the thing, though: all of the methods I mentioned work, but I shouldn’t have to resort to any of them, nor should you. And ultimately, none of these hacks actually solve the problem. However, for less than US$15, you can make it go away forever and finally banish that breaker bar to rusty automotive projects where it belongs.
The problem
The bike industry is obsessed with minimizing weight, particularly on higher-end products where weight is an easy thing to compare against competing products. Is X product stiffer/stronger/more aero/more durable than Y product? Hard to say. But is X lighter than Y? Hold on, let me crack out my handy dandy kitchen scale!
As such, it’s common to see higher-end product feature lower-density materials like carbon fiber, aluminum, and titanium – even in fasteners. It’s a relatively easy way to shave a few grams, the hardware looks good in marketing materials, and it also just sounds appealing. Those alternative hardware materials definitely increase the bling factor, but they’re not always the best choice for the task at hand from a functional perspective.
The US-based Federal Aviation Administration (FAA) and the National Aeronautics and Space Administration (NASA) have both published extensive guidelines on proper hardware selection and usage. Both of those fields are incentivized to minimize the weight of their crafts, which is why you almost never see airplanes or rockets made of iron or steel. In the case of spacecraft, it’s been estimated that it requires so much energy to escape Earth’s gravitational pull that it costs an extra US$1,000 to get every additional gram – one gram! – into orbit.
Even so, neither the FAA nor NASA is all that big on aluminum hardware.
“Do not use aluminum bolts or nuts in applications requiring frequent removal for inspection or maintenance,” reads the FAA guidelines. And, “Titanium and aluminum bolts have limited usage, primarily in the aerospace industry,” according to NASA.
The problem is that while aluminum is light, it’s also a relatively soft metal. If you overtighten an aluminum screw inside a steel part, I think we can all agree which of the two sets of threads will fail first. But when you tighten an aluminum screw inside an aluminum part – in this case, an aluminum crank bolt into an aluminum spindle – you essentially end up with two losing sides. It isn’t just a matter of tightening things so much that the threads strip, either. Aluminum threads are prone to galling, where tiny bits of material flake off and eventually clog up the tiny space between the two mating parts.
Anodized surfaces help (as SRAM has done here, at least with the bolt) as it hardens the surface and prevents little bits of material from sloughing off under high shear loads. But under high torque and with larger diameters – both of which apply here – the two halves can still practically weld themselves together. This likely explains why the specified tightening torque is a substantial (but still viable) 54 Nm, but the loosening torque is often way, way higher. Curiously, applying anti-seize to the threads helps, but not as much as I would have expected.
And the fix
Aluminum hardware costs more than steel stuff, and so it shouldn’t be at all surprising that SRAM uses steel crank bolts for its entry-level DUB stuff. But unless you care more about saving a few grams than how well something actually functions, it turns out that the steel bolt is what you want – and it turns out the steel assembly is not only wholly interchangeable with the aluminum one, but it’ll only cost you US$13.
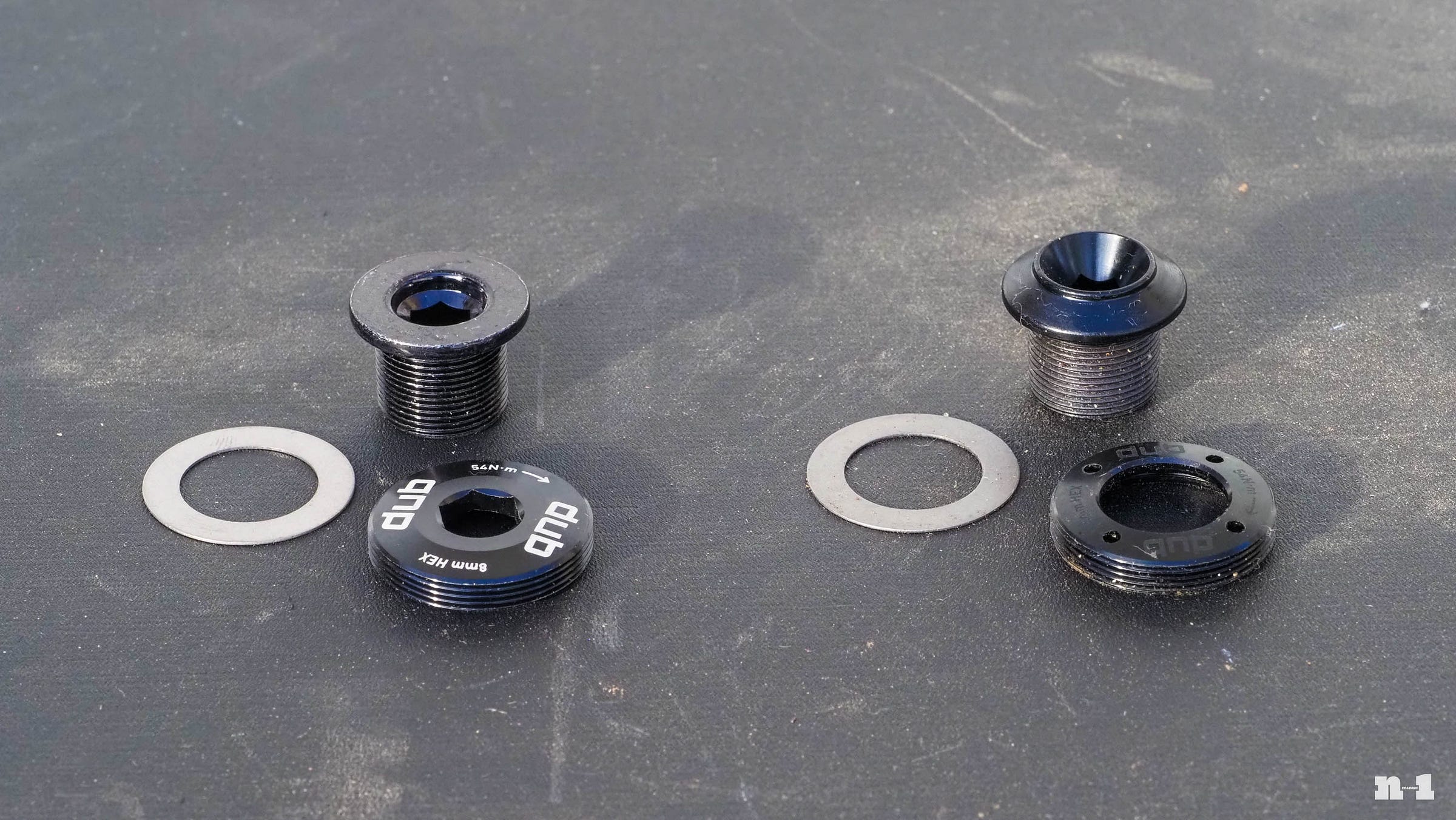
It’s a touch heavier at 31 g vs. 18 g, but it still includes a handy self-extracting cap (which is still aluminum) so it’s not like you’re losing anything in terms of convenience. And while I’m personally not a big fan of the bright laser etching found on the extractor cap that’s included with the steel bolt, that’s nothing a paint marker can’t easily fix.
Most importantly, the steel bolt tightens – and loosens! – exactly the way you want it to. The effort ramps up smoothly and predictably all the way to the 54 Nm spec, and you can undo it with nearly the same amount of effort, with no cheater bars, no pipes, no impact wrenches, no cursing, no calling your buddies for help, and no more bloody knuckles.
FYI, it’s SRAM part number 11.6118.066.000. And you’re welcome.
Feeling a bit of déjà vu? Guilty as charged; I’ve written about this before, about 3 1/2 years ago, in fact, when I was working for CyclingTips (RIP). It seems word of this fix still hasn’t gotten around as much as I think it should, though, so I decided it was worth repeating myself.
This is the sort of post I should probably reserve only for paid subscribers (I am trying to make a living here, after all). However, it’s such useful information that I think more people should have access to it so this one’s on me. But if this little tidbit of knowledge ended up making your day, please consider signing up.
When I first started working on spacecraft integration and test at JPL I was shocked there weren't 6/4 Ti fasteners everywhere, especially given how much attention is paid to mass budgets. Speaking with fastener and structural SMEs I quickly learned what you've summarized here: lightweight is great, but it has to work properly. The NASA flight fastener guide is a dense read (and fascinating if you're a nerd like me) but offers detailed insight into what materials play nice with each other. Perhaps SRAM can offer a DUB crank with Nitronic 60 thread inserts and an A286 fastener for the real aficionados among us ;)
I too use an automotive breaker bar on the DUB equipped bikes in my fleet, but have never resorted to the additional cheater pipe, etc. except for new bikes ostensibly assembled by gorillas at the factory. A liberal coat of Motorex 2000/Dura Ace grease on the thread interfaces, including fastener head, and properly* torquing with my trust ICON wrench (the working man's Snap On) results in a tight but not unbearable fit. (*don't get me started about proper use and storage of torque tools...)
Also, those damn self extracting caps are really good at working themselves loose on the trail. I put a dab of loctite blue on the threads when installing.
$1,000 to lift one extra gram into space, or $1,000 to drop one pound off your bike - at least that was the rough number back in my bike shop days.
Thank you for the tips James. This will surely prevent some occasional frustration.